All About Supply Chain Management
The supply chain is exactly what it sounds, the entire process from procuring the raw materials to delivering it to the end customer. This is achieved through effective planning and coordination across different sections of the business both external and internal. The core components that make up a basic supply chain are supply, operations, logistics and integration.
Supply
It is the beginning of the chain where a company gets its supply of raw materials to begin the manufacturing process. But supply does not stop at procuring goods and it also includes both upstream and downstream supply.
Operations
This component refers to people, process and equipment required for production and manufacturing. The chain consists of a lot of moving parts so, maximising the scope of operations helps move things along smoothly.
Logistics
Do not confuse supply chain with logistics. Even though the two seem similar, they could not be more different. The supply chain is the flow of products and services throughout the business (both upstream and downstream) and the linking of major business processes into a single high-performance business model. Logistics is the ‘muscle’ that helps these products and services get from point A to point B.
Integration
it is basically how well a supply chain is integrated with the business, that is to say, how smoothly the data flows between different departments of the business. Businesses nowadays, use specialised supply chain management software to give them more control and monitoring power over the whole process. Moreover, digital-era integrations provide more effective oversight of various moving parts and help the management take quick action where needed.
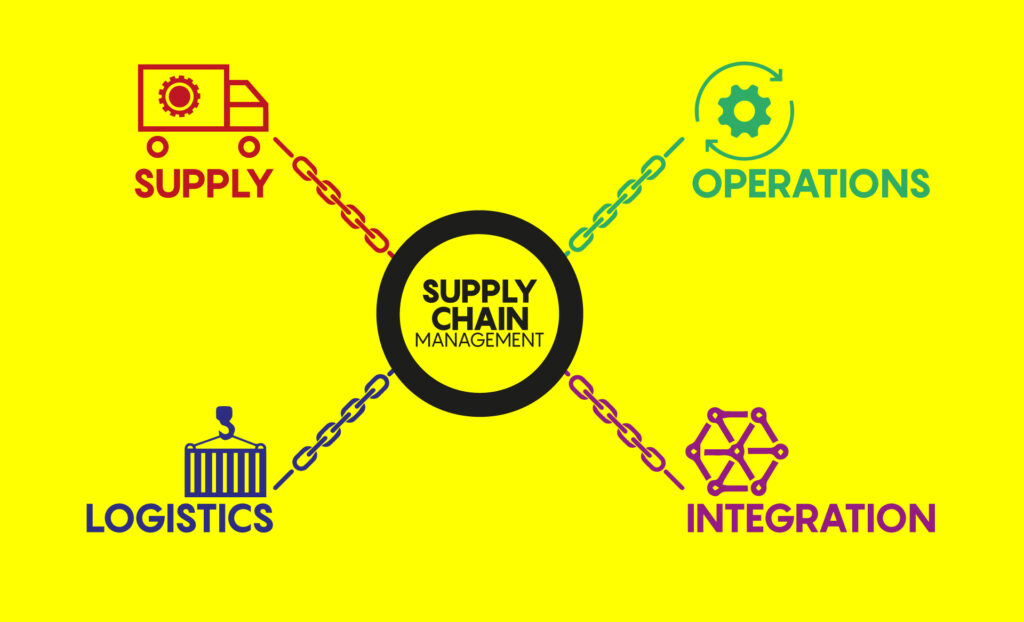
‘‘
The supply chain is a highly integrated and complex chain mechanism that is key to the daily functioning of businesses.
How Supply Chain Evolved
Supply chain management (SCM) had started in the colonial era, long before the term was coined in 1982. The New World was being discovered and shipping routes were being established. The need for a supply chain was ever-growing and so, a primitive form of such a chain was developed. The massive shipping routes and delivery systems were broken up into segments where more and more traders and suppliers came into play.
With the advent of the Industrial Revolution, the need for more efficiently mass-produced goods became necessary. This led to the development of the supply chain management to keep up with the sudden spike in demand. By the time Henry Ford had introduced his revolutionary car assembly line for maximum efficiency in 1913, the supply chain had nearly been perfected.
Later in the century, businesses were struggling to keep up with demand. As a solution to reduce cost while still meeting demand, businesses started to vertically integrate the chain of supply into their operations. They absorbed the supply chain from the top-down, so that they owned and controlled the sources, suppliers, manufacturing and so on. For example, newspaper publications that absorbed all aspects of the business from the supply of raw materials to the distribution of the final edition in order to have a better control of the chain of supply and the final price of the product.
The arrival of globalisation in the 1980s made integration and cross-communication that much easier with the aid of the internet. This grew into what we know today as ‘SCM 2.0’, where even the most complex of supply chains can be managed by companies both big and small, thanks to things like social media, digital democratisation and other collaborative platforms.
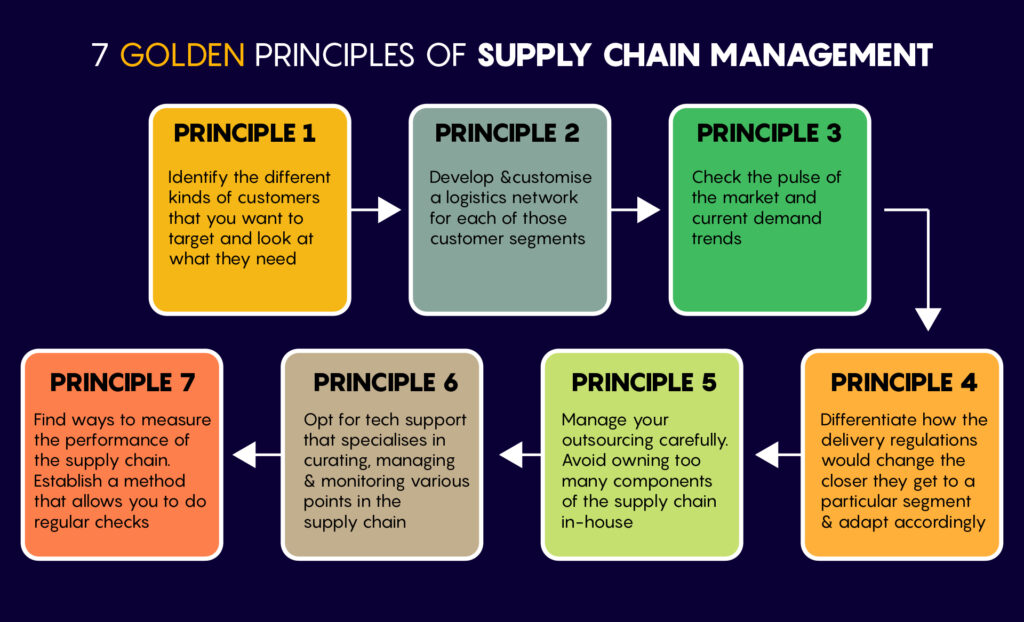
Seven Golden Principles
There are no hard and fast rules when it comes to managing a supply chain. Every business will need to find its feet and unique methodology, based on the type of service or product it provides. There are, however, seven principles to keep in mind if you want to play a long game.
Principle 1
Identify the different kinds of customers that you want to target and look at what they need. Adapt the supply chain according to those needs.
Principle 2
Develop and customise a logistics network for each of those customer segments so that their specific needs are met.
Principle 3
Check the pulse of the market and current demand trends. Identify the pattern and align your planning with the supply chain accordingly. The better your demand forecast is, the less likely the plan is to fail.
Principle 4
The further a product moves down the supply chain and the closer it gets to end users, the more the regulations change. For instance, if a product crosses an international boundary, it would have to meet certain regulatory compliances in the country of arrival. So, you need to differentiate how the delivery regulations would change the closer they get to a particular segment and adapt accordingly.
Principle 5
Manage your outsourcing carefully. Avoid owning too many components of the supply chain in-house. It is better if you keep just the core components, that is to say, what you absolutely need to have, and outsource everything else. Lessen the load on your internal teams as much as possible.
Principle 6
Opt for tech support that specialises in curating, managing and monitoring various points in the supply chain. It helps your business have a more transparent view of the processes. This will allow you to quickly identify the needs and improve the lacking areas.
Principle 7
Find ways to measure the performance of the supply chain. Establish a method that allows you to do regular checks. This will also help measure the customers’ responses to your efforts to meet demand.
‘‘
There is no set rule or principle in business, but it never hurts to have a strong set of guidelines to follow to make sure your efforts remain as uniform as possible.
Five Best Practices
Increase supply chain visibility
Allow your suppliers and distributors a transparent view of your business’s inventory needs so that they can easily identify where you are lacking, giving them ample time to prepare for future demands. Such real-time transparency allows not only better forecasting but a degree of autonomy for the supplier, which means less stress on the management.
Go for automation
It can be a boon or severely crippling if used in wrong places. Keep it as a rule of thumb to automate only where necessary. Machine-aided operations can greatly increase efficiency but if you fully rely on that, and something does go wrong the entire chain is affected.
For example, let us say you have a supply chain that is entirely dependent on the automation software, and suddenly the software malfunctions. You will be left sitting in the dark or at the very least struggling to keep business going smoothly till the software is up and running again.
IT check-ins
Have a regular check-up run by your IT department to make sure that everything is updated and running smoothly and that there are no technical glitches in the automation system. The IT team has an overall perspective of the goings-on in the business and this puts them in the unique position to sniff out problems.
Offer in-house training
Give your internal staff better training so that even if something goes awry, you will have covered all your bases internally. Brings down the chances of liability on your side of the fence.
Set up a project plan
You should implement a central framework to map risks and opportunities, elaborates the distribution, procurement and logistics, and facilitates cross-functional communication. This will act like a pivot based on which you can set new goals, milestones or even develop new strategies. Think of it as an anchor as you venture out into stormy weather.
To maximise the efficiency of your supply chain management, check out our article on ‘The 5 Ms of Management’ and understand the core elements crucial for every business.